Automated Box Packing System
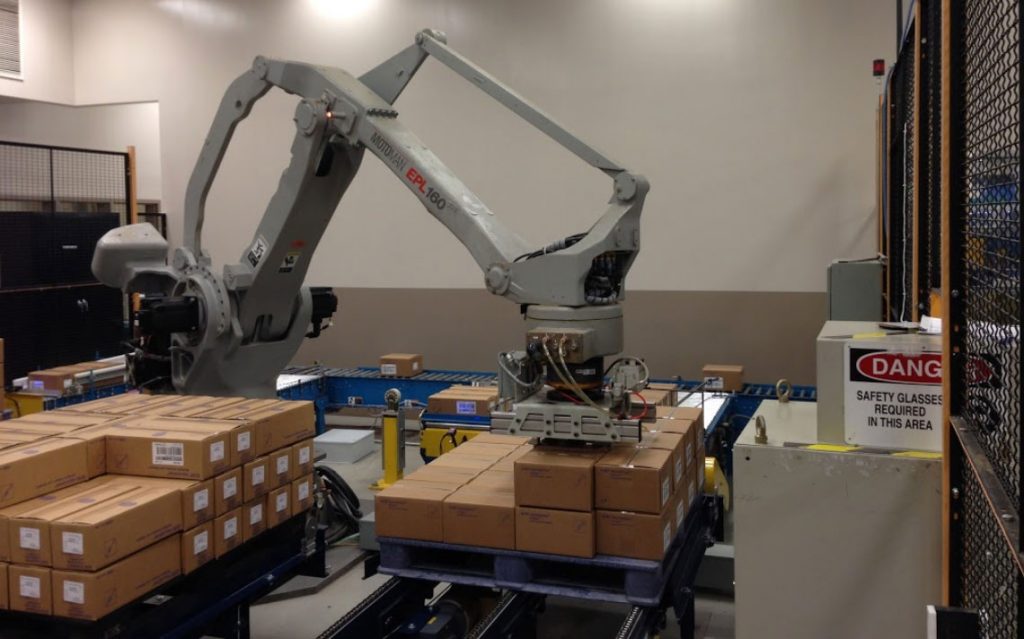
Medical Hard Goods Manufacturing Company
Challenges
- Customer’s existing box makers were out of date and proving unreliable.
- The new available box makers did not erect the boxes at the same elevation or in the same orientation.
- Existing conveyors could not be modified.
- Provide complete mechanical, electrical and PLC controlled solution with touch screen interface for fault recovery.
Goal
- Build automated box erectors and integrate them into the existing system, in keeping with originally planned downtime over a holiday shut down.
- Develop the boxes that produce a reliable, increased rate so operators downstream have a continuous supply of boxes without waiting.
- Create a very simple, intuitive fault recovery process so new operators can be easily trained and easily recover from mistakes when they occur.
Solutions
- Manufactured and fabricated two automated box erectors in two different sized boxes.
- Created an integrated packing process that orients the box on its side and presents the box in the required format for that run.
- Provided a cost-effective pneumatic gantry to pick and place boxes using a vacuum generator and suction cups.
- Elevated the packing boxes and moved them horizontally to position over conveyor and place on take away conveyor.
Successes
- Installed equipment and provided control system integration into customer’s existing system.
- The custom manufactured solution now presents the boxes in a better ergonomically correct horizontal position.
- Suction cups provided a non-marking way to relocate boxes to an improved elevation level.
- The two different box erectors and lifting equipment were brought on line, on time and on budget to meet the customer’s critical schedule.